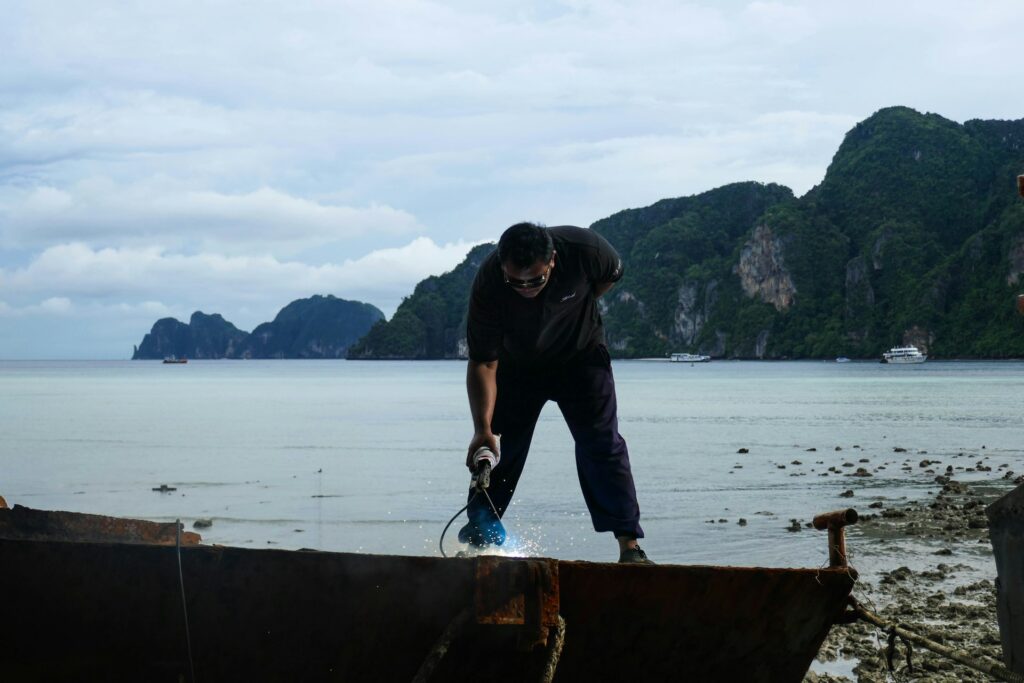
Underwater welding and repair have come a long way since their inception. Today, innovative techniques are pushing the boundaries of what’s possible in marine construction and maintenance.
This blog post dives into the advanced methods being used in underwater repair, focusing on how innovation benefits industries and professionals alike.
You’ll learn about various underwater repair techniques, modern repair methodologies, and the latest technologies driving these practices. Along the way, we’ll look at real-world examples and industry testimonials to illustrate the impact of these innovations on the field.
The Basics of Underwater Welding
Underwater welding is a unique discipline that combines traditional welding skills with specialized techniques suited to underwater environments. The primary methods used include:
- Wet Welding – Performed directly in the water, wet welding uses waterproof electrodes and is known for its cost-effectiveness and flexibility.
- Dry Welding – Also called hyperbaric welding, this technique involves creating a dry chamber around the weld area for a more controlled environment.
Understanding these basic methods is crucial as they form the foundation upon which more advanced techniques are built.
Wet Welding Explained
Wet welding is often the go-to method for quick, in-situ repairs. It allows for work to be completed without the need to dewater the area, making it a cost-effective solution. However, it has its drawbacks, such as an increased risk of hydrogen-induced cracking.
Dry Welding Advantages
Dry welding, on the other hand, offers the advantage of a controlled environment, resulting in higher-quality welds. This method is particularly useful for critical repairs where weld integrity is paramount. The downside is the higher cost and complexity involved in setting up the hyperbaric chamber.
Safety Considerations
Both methods require rigorous safety protocols. Divers must be well-trained and equipped with specialized gear to handle the unique challenges of underwater welding, such as limited visibility and the potential for electrical hazards.
Advanced Techniques in Underwater Welding
Innovations in underwater welding have brought about advanced techniques that improve efficiency, safety, and quality. Here are some of the latest advancements:
Friction Stir Welding
Friction stir welding (FSW) is a solid-state joining process that generates heat through friction between the welding tool and the workpiece. This technique is gaining traction in underwater applications due to its ability to produce high-quality welds with minimal defects.
Laser Welding
Laser welding uses focused laser beams to join materials underwater. This method offers precise control and can be automated, making it ideal for complex repairs and small-scale applications.
Ultrasonic Welding
Ultrasonic welding employs high-frequency ultrasonic vibrations to create the weld. This non-traditional method is beneficial for joining dissimilar materials and can be performed quickly, reducing downtime.
Repair Techniques Revolutionizing the Industry
In addition to welding, innovative repair techniques are enhancing the capabilities of underwater maintenance. These methods ensure that structures remain safe and functional with minimal disruption.
Epoxy Injection
Epoxy injection involves injecting a specialized epoxy resin into cracks or voids within structures. This technique is particularly effective for repairing concrete and steel, providing a durable and corrosion-resistant solution.
Carbon Fiber Wrapping
Carbon fiber wrapping strengthens and stabilizes damaged areas by applying high-strength carbon fiber fabric soaked in resin. This method is lightweight, easy to apply, and provides exceptional reinforcement.
Cathodic Protection
Cathodic protection is a corrosion prevention technique that uses sacrificial anodes for impressed current systems to protect metal structures. This method extends the lifespan of underwater assets by preventing rust and degradation.
The Role of Technology in Underwater Welding and Repair
Technology plays a pivotal role in advancing underwater welding techniques. From robotics to artificial intelligence, here are some of the technological innovations making waves in the industry.
Remotely Operated Vehicles (ROVs)
ROVs are invaluable tools for underwater inspections and repairs. These remotely controlled machines can access hard-to-reach areas and perform tasks with precision, reducing the need for human divers.
Robotics and Automation
Robotic systems equipped with welding and repair capabilities are transforming the industry. Automated welding robots can perform complex tasks with high accuracy, improving productivity and safety.
Artificial Intelligence and Machine Learning
AI and machine learning algorithms are being used to analyze data from underwater inspections and predict maintenance needs. This proactive approach ensures timely repairs and reduces the risk of unexpected failures.
Real-World Applications and Success Stories
To understand the impact of innovation, let’s look at some real-world examples and success stories.
Central States Underwater Services
It is the leading provider of underwater welding and repair solutions. Their use of advanced techniques like friction stir welding and epoxy injection has set new standards in the industry. Clients have reported significant improvements in repair quality and reduced downtime, thanks to the innovative methods employed by Central States Underwater Services.
Offshore Oil Rigs
Offshore oil rigs present some of the most challenging environments for underwater welding and repair. The use of ROVs and robotic systems has revolutionized maintenance operations, ensuring the safety and integrity of these critical structures.
Naval Applications
The naval sector also benefits from advanced underwater welding techniques. Submarines and ships undergo regular maintenance using methods like laser welding and cathodic protection, ensuring their readiness for deployment.
The Future of Underwater Welding and Repair
The future of underwater welding and repair looks promising, with continuous advancements in technology and techniques. Here are some trends to watch for:
Increased Automation
Automation will continue to play a significant role, with more sophisticated robotic systems and AI-driven solutions being developed. This trend will enhance efficiency and safety, reducing the reliance on human divers.
Sustainable Practices
Sustainability is becoming a priority in the industry. Techniques that minimize environmental impact, such as eco-friendly epoxy resins and carbon-neutral welding processes, are gaining traction.
Enhanced Training Programs
As techniques and technologies evolve, so too must the training programs for underwater welders and repair technicians. Advanced simulation tools and virtual reality training are providing more effective and immersive learning experiences.
Conclusion
Innovative techniques in underwater welding and repair are transforming the industry, offering improved efficiency, safety, and quality. From friction stir welding to epoxy injection, these advancements are setting new standards and driving the future of marine maintenance.
For businesses and professionals looking to stay ahead, it’s essential to keep up with innovation and explore their potential applications. Whether you’re a small business owner or a large corporation, investing in advanced underwater repair techniques can provide a significant competitive advantage.
To learn more about how Central States Underwater Services can help you implement these cutting-edge methods, visit their website and discover the possibilities.
Innovations in underwater welding and repair are not just shaping the future, they’re here now, making waves and setting new benchmarks for excellence. Don’t miss out on the opportunity to leverage these advancements and take your operations to the next level.
Last modified: October 12, 2024