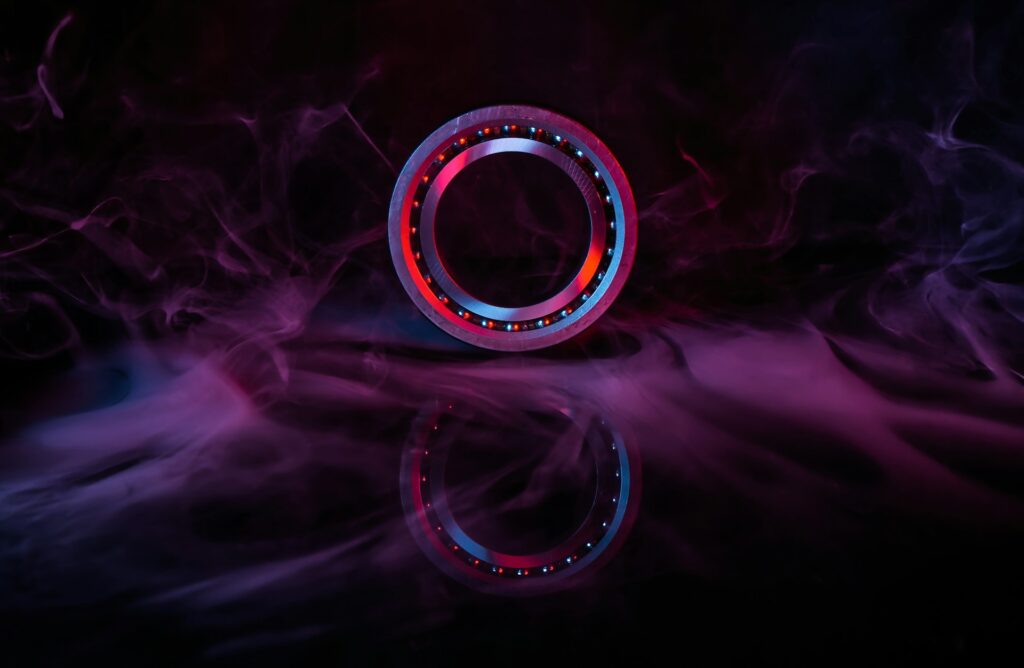
Ball bearings are the silent workhorses of modern machinery, enabling smooth rotation and reducing friction across countless applications.
From industrial equipment to automotive systems, these precision components play a crucial role in operational efficiency.
Yet many maintenance professionals overlook the specific care requirements that can dramatically extend bearing lifespan and prevent costly equipment failures.
Proper bearing maintenance isn’t just about following a schedule—it’s about understanding the unique demands of different bearing types and implementing targeted strategies that address their specific vulnerabilities.
This comprehensive approach to equipment care can transform your maintenance program from reactive to proactive, delivering measurable improvements in both performance and cost efficiency.
Understanding Ball Bearing Fundamentals
Ball bearings consist of precisely manufactured components that work together to minimize friction and support loads.
The inner and outer races, rolling elements, and cage or separator each serve specific functions that contribute to overall bearing performance.
When any of these components experiences wear or damage, the entire bearing assembly can fail.
Different bearing types require different maintenance approaches. Mounted linear ball bearings, for instance, operate under unique conditions that demand specialized attention.
These bearings experience linear motion rather than rotational movement, creating distinct wear patterns and lubrication requirements that differ significantly from traditional radial bearings.
Temperature fluctuations, contamination, and improper loading represent the primary threats to bearing longevity.
Understanding these factors allows maintenance teams to develop targeted prevention strategies that address the root causes of bearing failure rather than simply treating symptoms.
Lubrication Strategies for Extended Life
Proper lubrication forms the foundation of effective bearing maintenance.
The lubricant creates a protective film between moving surfaces, reducing friction and preventing metal-to-metal contact that leads to premature wear.
However, both over-lubrication and under-lubrication can cause significant problems.
Selecting the Right Lubricant
Lubricant selection depends on operating conditions, temperature ranges, and speed requirements.
High-temperature applications require lubricants with superior thermal stability, while high-speed operations demand low-viscosity options that minimize churning losses.
Environmental factors such as moisture exposure or chemical contamination also influence lubricant choice.
Synthetic lubricants often provide superior performance compared to conventional options, offering better temperature stability, longer service intervals, and improved protection against oxidation.
While the initial cost may be higher, the extended service life and reduced maintenance requirements typically justify the investment.
Relubrication Intervals and Techniques
Establishing appropriate relubrication intervals prevents both lubricant starvation and over-lubrication.
Operating temperature, speed, and load conditions all influence the optimal relubrication frequency.
Bearings operating under severe conditions may require more frequent attention, while those in mild environments can operate longer between service intervals.
Proper relubrication technique involves removing old lubricant before applying fresh material. This prevents contamination and ensures that the new lubricant can perform effectively.
Automated lubrication systems can provide consistent, measured amounts of lubricant at predetermined intervals, reducing human error and improving maintenance consistency.
Contamination Prevention Methods
Contamination represents one of the most significant threats to bearing performance. Dirt, moisture, and foreign particles can cause abrasive wear, corrosion, and premature failure.
Implementing comprehensive contamination control measures can extend bearing life by several times compared to unprotected installations.
Sealing and Protection Systems
Effective sealing prevents contaminants from entering the bearing housing while allowing for proper lubrication and thermal management.
Contact seals provide superior protection but generate additional friction, while non-contact seals offer lower friction at the expense of some protection capability.
Multiple seal configurations can provide enhanced protection in severe environments.
Labyrinth seals combined with contact seals create a multi-barrier system that prevents contamination while maintaining operational efficiency.
Regular seal inspection and replacement prevent small problems from becoming major failures.
Environmental Controls
Controlling the operating environment reduces contamination exposure and creates more predictable operating conditions.
Air filtration systems, positive pressure enclosures, and temperature control all contribute to improved bearing performance and extended service life.
Regular cleaning of equipment and surrounding areas prevents the accumulation of contaminants that could eventually find their way into bearing housings.
Establishing clean work practices during maintenance activities also prevents contamination introduction during service operations.
Monitoring and Inspection Techniques
Proactive monitoring allows maintenance teams to identify potential problems before they result in bearing failure.
Vibration analysis, temperature monitoring, and lubricant sampling provide valuable insights into bearing conditions and performance trends.
Vibration Analysis Applications
Vibration analysis can detect bearing defects in their early stages, allowing for planned maintenance rather than emergency repairs.
Different bearing defects produce characteristic vibration signatures that trained analysts can identify and interpret.
Regular vibration monitoring establishes baseline conditions and tracks changes over time. Portable vibration analyzers make it practical to monitor large numbers of bearings on a regular schedule.
Automated monitoring systems provide continuous surveillance of critical equipment, alerting maintenance personnel to developing problems before they cause unexpected failures.
Temperature Monitoring Benefits
Temperature monitoring provides early warning of lubrication problems, excessive loading, or contamination issues.
Sudden temperature increases often indicate developing problems that require immediate attention. Gradual temperature increases may signal the need for relubrication or other maintenance actions.
Infrared thermography allows for non-contact temperature measurement and can identify hot spots that indicate bearing problems.
Regular thermal imaging surveys can detect problems that might otherwise go unnoticed until failure occurs.
Installation and Handling Best Practices
Proper installation and handling practices prevent damage that could compromise bearing performance from the very beginning.
Even minor installation errors can significantly reduce bearing life and create ongoing maintenance challenges.
Mounting Procedures
Proper mounting requires appropriate tools and techniques to prevent bearing damage during installation.
Heating methods for interference fits must be carefully controlled to avoid overheating that could affect material properties.
Hydraulic and mechanical mounting tools apply force evenly and reduce the risk of damage.
Shaft and housing preparation ensures proper fit and alignment. Surface finish, dimensional accuracy, and cleanliness all affect bearing performance and longevity.
Taking time to verify these conditions before installation prevents many future problems.
Storage and Handling Considerations
Proper storage protects bearings from contamination and damage before installation.
Climate-controlled storage areas prevent moisture condensation and temperature fluctuations that could affect bearing materials.
Proper packaging and handling procedures prevent physical damage and contamination.
Inventory rotation ensures that bearings are used within their recommended storage life.
Some bearing types and lubricants have limited shelf life, and using aged components can result in premature failure even when installation and operation are perfect.
Troubleshooting Common Issues
Understanding common bearing problems and their causes enables more effective troubleshooting and prevention strategies.
Many bearing failures follow predictable patterns that can be identified and addressed before they cause equipment damage.
Wear Pattern Analysis
Different failure modes produce characteristic wear patterns that provide valuable information about the underlying cause.
Fatigue spalling, abrasive wear, and corrosion each create distinct signatures that experienced technicians can interpret.
This information guides corrective actions and helps prevent similar problems in the future.
Documenting wear patterns and failure modes creates a valuable database for future reference.
This information helps identify recurring problems and evaluate the effectiveness of different maintenance strategies.
Load and Alignment Considerations
Improper loading and misalignment cause significant bearing stress and reduced life.
Understanding load ratings and application factors helps ensure that bearings are properly sized for their intended service.
Regular alignment checks verify that equipment remains within acceptable tolerances.
Thermal expansion and equipment settling can affect alignment over time. Establishing regular alignment verification procedures prevents gradual changes from causing bearing problems.
Flexible coupling systems can accommodate minor misalignments while protecting bearings from excessive stress.
Optimizing Your Maintenance Program
Effective bearing maintenance requires a systematic approach that addresses all aspects of bearing care.
Regular inspections, proper lubrication, contamination control, and condition monitoring work together to maximize bearing life and equipment reliability.
Developing standardized procedures ensures consistency across different maintenance personnel and equipment types.
Training programs help maintenance staff understand the importance of proper procedures and develop the skills needed for effective bearing care.
Documentation and record-keeping provide valuable insights into bearing performance trends and maintenance effectiveness.
This information guides program improvements and helps justify maintenance investments through demonstrated cost savings and improved reliability.
Regular program evaluation identifies opportunities for improvement and ensures that maintenance practices remain current with evolving technology and industry best practices.
Continuous improvement approaches help organizations achieve progressively better results from their longevity tips and maintenance investments.
Last modified: July 14, 2025